Imagine having the capability to fully understand and validate the capacity of a depot before introducing a fleet or making the changes to the timetable. Imagine quantifying the loss in maintenance time due to depot limitations. Imagine being able to show tangible benefits for infrastructure and flow improvements to validate a business case.

IPEX has developed a bespoke depot modelling tool that enables operators, designers, builders, and funders to fully understand their depots, analyse operational and fleet composition scenarios, identify bottlenecks, validate operational capability and efficiency, and support business cases for investments in depot expansions or enhancements.
The need for depot modelling
All train maintenance depots are unique, defined by their geography, topography, footprint, layout, levels of electrification, fleets maintained, and facilities – from stabling, servicing, light maintenance and cleaning activities, through to full overhaul facilities.
Current depot owners and operators are all too familiar with the bottlenecks in their operation. These can vary from resource constraints, facility constraints, to movement restrictions based on track geometry and train movement protection. The effects of these constraints may impact different depots in different ways. A robust business case is essential before expensive improvements or adaptations can take places. Being able to test improvements with different permutations at a design stage enables the quantification and maximisation of the benefits of any proposed solution. These may include a reduction in unnecessary movements, an increase of maintenance time enabling a focus on defect clearance, more flexibility to react to unscheduled arrivals and departures, or simply and improvement in capacity.
The modelling solution
Depot modelling provides confidence when operators and maintainers are introducing: new fleets to new depots, new fleets to existing depots, or new timetables to existing depots. It also provides proof of concept when changing depot layout or capability, providing full understanding of current depot static and dynamic capacity. It also provides an opportunity during business case and feasibility study stages of projects to analyse depot requirements enabling the most efficient and cost effective solutions to be designed.
Depot modelling validates a depot’s capability to process the demands of arrivals and their corresponding workflows including for reception or fuel point exams, train wash, cleaning, maintenance, repairs and fault finding, train and driver prep, and movements around the depot.
IPEX has a fully developed and validated depot modelling tool which can be configured for any depot type, new or existing. IPEX’s approach involves observing a typical busy shift (often at night), to record a baseline flow and activity schedule. By modelling activities for each arrival based on standard times, a ratio of actual touch time possible versus touch time achieved (the efficiency of the depot flow) is measured. With the baseline of movements and activities in each area of the depot modelled, improvements can be modelled and then analysed through workshops held with the client team and IPEX’s expert support.
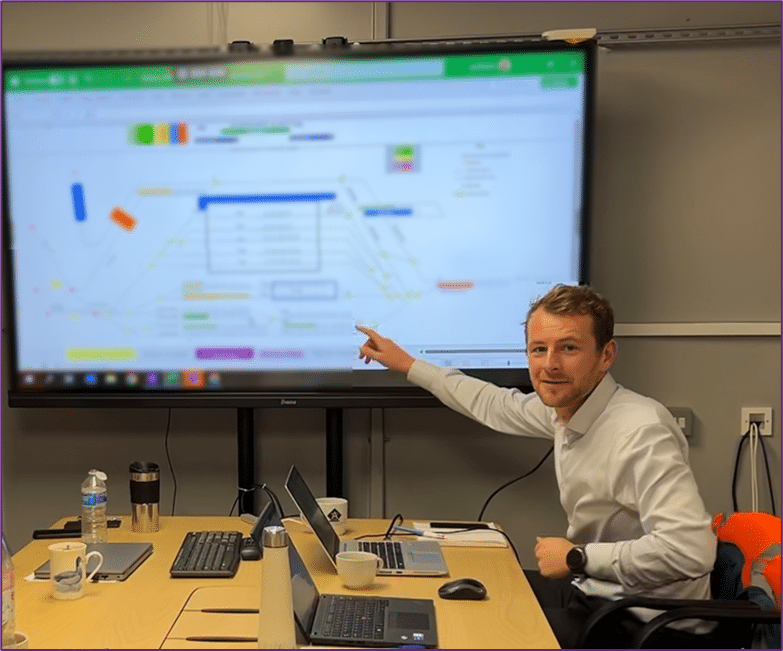
Using the model
The outputs from depot modelling bring understanding of the robustness of the depot to achieve the required maintenance activities and on time departures, a key performance indicator. By simulating a 24-hour period in 5 minute increments, IPEX’s tool will identify bottlenecks in depot processes or movements. These bottlenecks occur especially during peak periods of activity at night. The modelling tool enables the optimisation or creation of redundancy in critical areas. These improvements are not always apparent during day-to-day depot operations management, and the model enables off-site evaluation of different improvement strategies without the risk of having to physically trial them in active service.
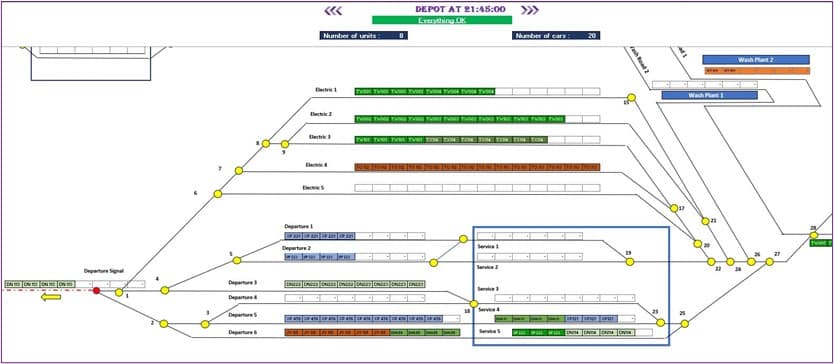
IPEX’s depot capacity modelling tool is built with configurarable content based on each client’s needs. On completion of the initial depot modelling development, the client is given the model and IPEX can train depot teams to use the model to enable them to validate future operational timetables, mainline blockades, or depot blockades during maintenance/ improvement works.
Case study – UK train operating company
IPEX has been retained by a British train operating company to carry out depot flow modelling. For each location, the IPEX team spent time on depot during the peak activity periods (night shift), and then built a bespoke model for each case. The models have then been used to consider improvements, with several iterations of the model used to trial such improvements. Headline findings have included:
- Planned additional stabling roads reduced in number having found flow efficiencies which removed the reliance on, and need for, one of the additional roads. The planned roads included significant earthworks and piling, and the reduction in roads significantly reduced the capital cost of the works.
- Several flow inefficiencies found in a depot which, when rectified, are likely to reduce the extent of depot expansion currently being considered.
- Analysis of current depot and its constraints has assisted in validating the business case for depot improvement and expansion works.
Get in touch
Trust us to accelerate your vision
Established in 2003, IPEX has a wide client and project base in global rail and transport consultancy. Our team has a combined wisdom of over 200 years’ working with major blue chip rail organisations, covering all aspects of rail operations, maintenance, and projects. Talk to us today and see how we can help you.
This site is protected by reCAPTCHA and the Google Privacy Policy and Terms of Service apply.