Independent Depot Capacity Assessment
Highly Utilised Depot in North of England
The overview
IPEX undertook an independent capacity assessment of a highly utilised depot in the North of England to determine the quantity of additional units which it could accommodate without compromising the existing customer fleets or pre-existing servicing contracts.
Our client’s challenge
The client was holding commercial discussions (with 3rd party operators) regarding the stabling and servicing of additional units at the depot. Multiple rolling stock types and configurations were being considered for both servicing and stabling. It was critical to understand if the depot could accommodate any additional units, and how many could be accepted without compromising the existing customer fleets at the depot, which held pre-existing servicing contracts, or exceeding total depot capacity.
- Assessed current stabling and servicing capacity
- Evaluated the impact of adding additional units
- Explored the possibility of stabling and servicing units of a different configuration
- Identified any needed upgrades to processes or infrastructure
- Defined how those upgrades would affect overall capacity
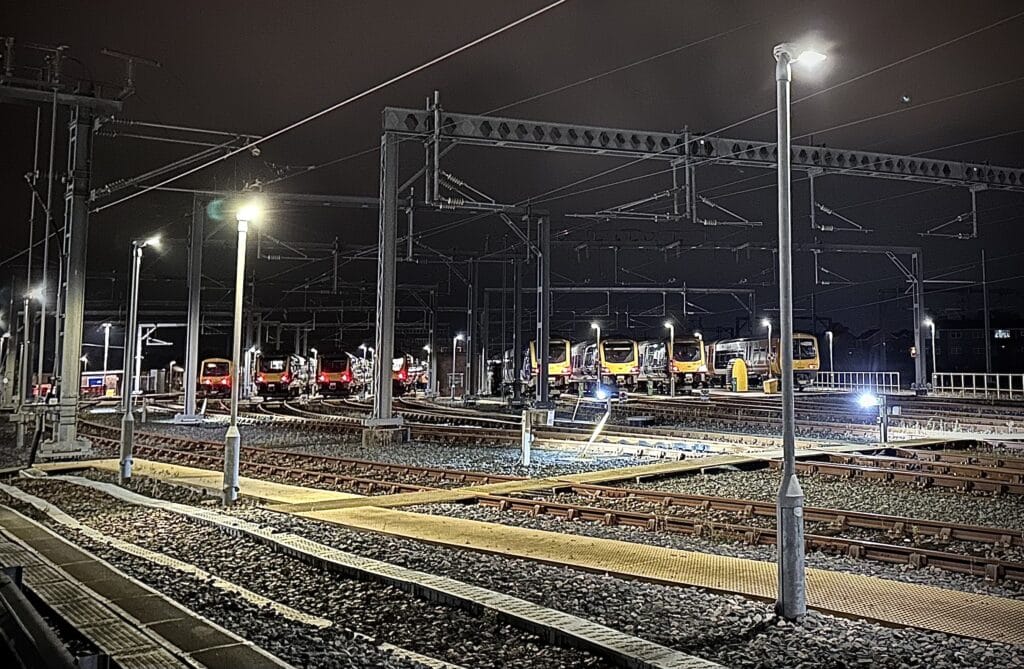
Our response and value to the client
The response
IPEX performed an independent evaluation of the depot stabling and servicing capacity by applying its proven methodology to create a bespoke user-friendly depot flow model specific to the depot. The model was built up from a proven set of IPEX concepts using a model template and a set of modelling inputs and assumptions. The principles of the modelling methodology are guided by IPEX’s extensive practical experience in depot management and layout design and has been used successfully by IPEX across several existing and new depots.
The assignment involved using the modelled scenario to demonstrate depot capacity, flow rates and optimisation options (in relation to both processes and infrastructure changes), in order to demonstrate clear and evidence-based conclusions to the client. IPEX also considered other process improvement ideas to extend capacity, bringing extensive experience and best practice from depot management and operations across the UK and overseas.
The output was formed as an extensive report, and supporting depot model, which explored current capacity, available capacity, and ability for it to potentially be utilised by other parties. Where limitations were identified, process or infrastructure enhancements were also proposed.
The value to the client
IPEX’s output informed the client’s commercial discussion with interested parties with regard to gaining access to the depot for stabling and servicing of additional rolling stock. The client also benefited from having a validated and verified depot modelling tool for the depot, and supporting analysis which incorporated and provided:
- Analysis of the depot and sidings capacity;
- Capacity for flow rates through key areas of the depot;
- Concise visibility of pinch points in the depot flow;
- Consideration of the interactions at bottleneck points within the depot;
- Critical path process and maximum downtimes for key processes before disrupting the normal depot flow;
- The essential depot facilities, equipment, and criticality of their normal function;
Simulation of additional arrivals in a theoretical future timetable; - A means of assessing and prioritising the available options (associated with process and infrastructure / facility) to increase capacity and depot flow efficiency in terms of impact, cost, complexity, and ease of implementation; and
- A means of assessing future changes (such as timetable changes) using the model, which was handed over to the client by IPEX (with training provided).